Understanding the Power of Prototype Molding in Metal Fabrication
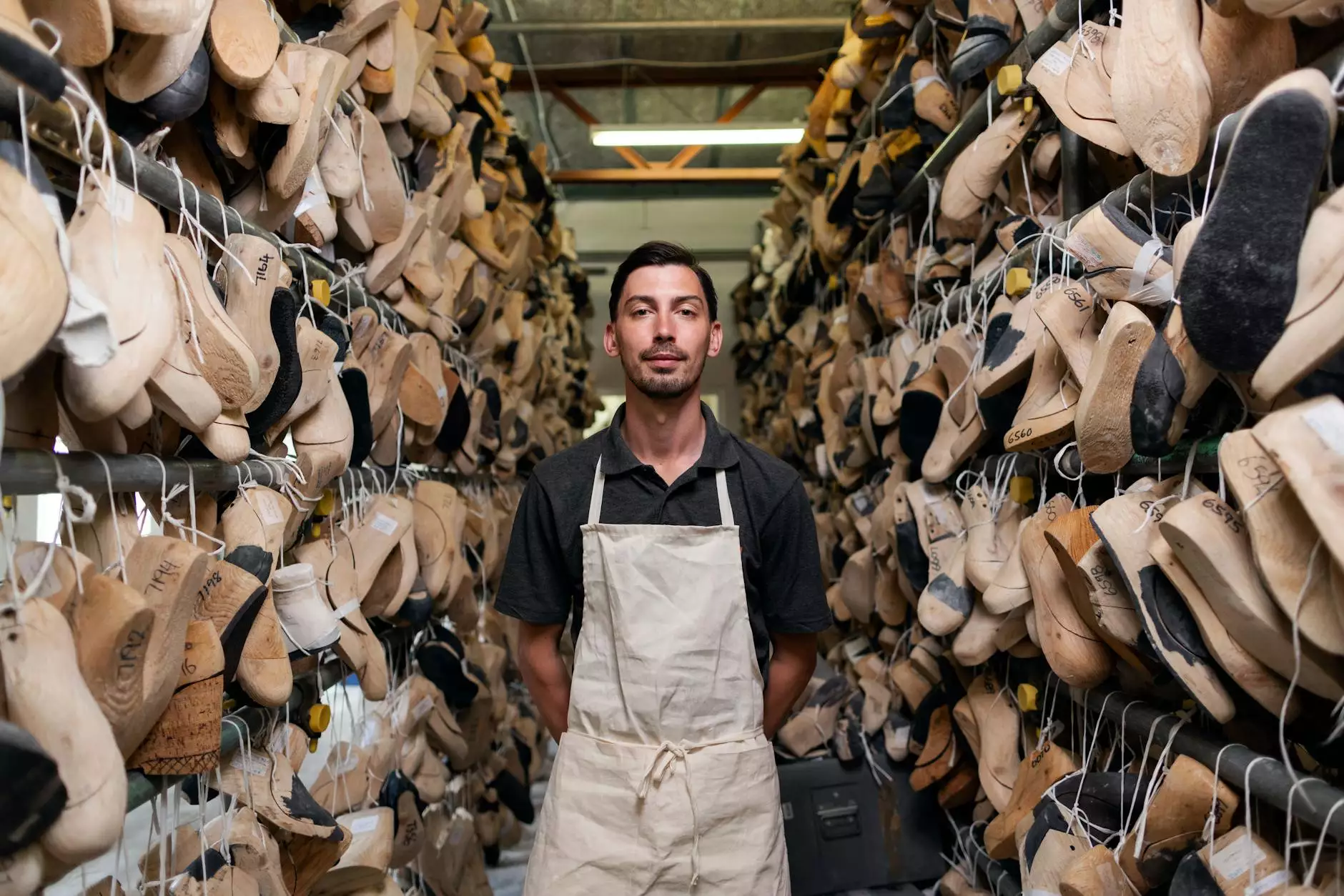
In the ever-evolving landscape of the manufacturing sector, prototype molding serves as a cornerstone for innovation, precision, and efficiency. As industries strive to keep pace with advancing technologies, the demand for quality prototype molding has surged. In this article, we will delve into the details of prototype molding and its significance in the realm of metal fabrication.
What is Prototype Molding?
Prototype molding is a manufacturing process that allows businesses to create prototypes of parts or products before mass production. This method is particularly crucial in metal fabrication, where precision and understanding of the material's behavior are key to successful outcomes. By utilizing this technique, manufacturers can test and iterate their designs without the substantial costs associated with full-scale production.
Key Benefits of Prototype Molding
The advantages of implementing prototype molding in your manufacturing process are manifold:
- Cost Efficiency: By creating a prototype, businesses can identify design flaws and make necessary adjustments before incurring the high costs of a full production run.
- Reduced Time to Market: Rapid prototyping techniques enable faster iterations, allowing companies to bring products to market more quickly.
- Enhanced Design Flexibility: Changes to the design can be made with minimal lead time, ensuring adaptability to market demands.
- Improved Product Quality: By testing prototypes, manufacturers can ensure quality and functionality, leading to higher customer satisfaction.
The Role of Metal Fabricators in Prototype Molding
Metal fabricators play a crucial role in the prototype molding process. Understanding the unique characteristics of metals, including their strength, malleability, and thermal properties, is essential for producing effective and reliable prototypes. Here are some ways that metal fabricators contribute:
1. Material Selection
Choosing the right materials is fundamental in ensuring that prototypes behave as expected. Skilled metal fabricators understand the advantages/limitations of various metals such as:
- Aluminum: Lightweight yet strong, ideal for many applications.
- Steel: Offers durability and strength, often used in heavy-duty applications.
- Brass: Known for its corrosion resistance, perfect for aesthetic components.
2. Advanced Techniques
Reputable metal fabricators leverage cutting-edge techniques in prototype molding, including:
- CNC Machining: Computer Numerical Control (CNC) machining allows for high precision in cutting, shaping, and finishing metal components.
- 3D Printing: Rapid prototyping via 3D printing can expedite the testing phase significantly.
- Laser Cutting: This technology provides unparalleled precision in cutting complex shapes and designs.
The Process of Prototype Molding
The prototype molding process involves several key steps, ensuring a clear path from initial concept to final prototype:
1. Concept Development
The journey begins with the design phase, where concepts are drafted based on customer needs and market research. This stage lays the foundation for the prototype.
2. Design Verification
Utilizing CAD (Computer-Aided Design) software, designers create detailed models. This ensures that every aspect of the prototype is considered before moving forward.
3. Prototype Manufacturing
Once the design is finalized, the prototype is manufactured using the chosen materials and techniques. This stage might involve multiple iterations based on testing results.
4. Testing and Evaluation
After manufacturing, the prototype undergoes rigorous testing to evaluate its performance against design specifications. This feedback loop is essential for refining the product.
Real-World Applications of Prototype Molding
The capabilities of prototype molding extend across various industries, including:
Aerospace
In the aerospace sector, precision is paramount. Prototyping allows for rigorous testing of components that must meet specific safety and performance criteria.
Automotive
Automakers utilize prototype molding to design and test parts efficiently, reducing the cycle time from concept to production.
Consumer Electronics
With the fast-paced nature of consumer electronics, manufacturers rely on prototyping to ensure their products are competitive and meet consumer expectations.
Choosing the Right Partner for Prototype Molding
When selecting a vendor for your prototype molding needs, consider the following:
- Experience: Look for a partner with a proven track record in your industry.
- Technology: Ensure they employ the latest technologies to deliver high-quality prototypes.
- Support: Choose a supplier that offers robust support throughout the design and prototyping process.
DeepMould.net: Your Trusted Source for Prototype Molding
At DeepMould.net, we specialize in delivering top-tier prototype molding solutions tailored to meet the unique needs of our clients in the metal fabrication sector. Our team of experienced engineers and fabricators is dedicated to ensuring that your prototypes are manufactured with precision, enabling you to focus on innovation and growth.
Why Choose Us?
- Expertise in a wide range of metals and fabrication techniques.
- Commitment to quality assurance and customer satisfaction.
- State-of-the-art facilities equipped with advanced machinery.
Conclusion
In conclusion, mastering prototype molding is essential for any business looking to excel in the competitive field of metal fabrication. It provides the ability to innovate rapidly, ensuring that products meet high standards of quality and performance. Partnering with experienced metal fabricators like DeepMould.net can significantly enhance your prototyping efforts, paving the way for successful product launches and business growth.
Invest in prototype molding today, and watch your ideas transform into reality with efficiency and precision.